Lexi Guignard
3D printing is a fascinating way to create three-dimensional objects. The process is also known as additive manufacturing, where material is added to create a model (as opposed to subtractive manufacturing such as milling). 3D printing is useful for prototyping, as it minimizes the time and cost of creating complicated shapes for specific purposes. In all forms of 3D printing, the model is sliced horizontally and each layer becomes a flattened image. Each layer of material is stacked on top of each other to create the object. Different kinds of 3D printing use different materials and methods of building, and the variety of ways to 3D print have many useful applications.
Fused Deposition Modeling (FDM)
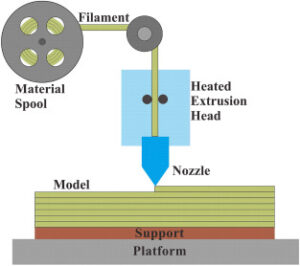
In fused deposition modeling (FDM), a heated nozzle feeds plastic filament to an extrusion head, which increases in temperature and softens the material before placing it. The material cools during the process of printing, so the build platform gradually descends as the model quickly cools and accepts another layer. FDM has low lead times and is cost-effective, however, it has low dimensional accuracy and is best suited for prototyping over critical applications.
Material Jetting
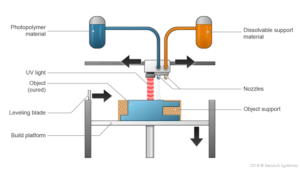
Material jetting uses print heads to deposit layers of liquid material onto a build platform. Each layer is cured by ultraviolet light before the next layer is produced. The simplest mechanism is an assembly of the printheads and UV light that immediately deposit and cure as the apparatus goes back and forth over the build platform. Material jetting relies on support structures, however, the printheads can print the support structures with a water-soluble substance to easily remove them. The printing method can print full-color parts, but the process is costly and the object is brittle and degradable.
VAT Photopolymerization
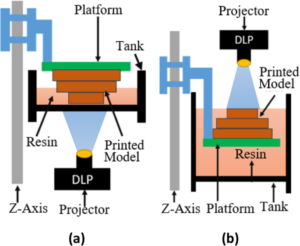
Vat photopolymerization is a chemically complex form of 3D printing. It involves filling a vat with a photopolymer and using a light source to harden the material. Photopolymers are materials that react to radiation in the ultraviolet range of wavelengths; when the materials chemically react, they become solid. Vat photopolymerization can use different light sources, including UV, visible light, gamma rays, x-rays, and electron beams. Photopolymers consist of photoinitiators, reactive diluents, flexibilizers, stabilizers, and liquid monomers. When the photoinitiator undergoes chemical change under radiation, it reacts with the monomer. The monomer reacts with other monomers, creating polymers. Polymers have covalent bonds so they are bonded on a molecular level. Objects created with vat photopolymerization have a stronger layer bond than FDM print and can print at a much higher resolution than FDM. The printing process for Vat photopolymerization differs by the light source and how the material is cured. Stereolithography, or SL, is a precise method of printing, as it uses a UV laser to trace the shape of each layer for a print. Digital light processing, or DLP, projects an entire layer on the photopolymer, printing at a faster rate than SL. Each method can use a top down or bottom approach for printing. Top down printing keeps the build platform in a vat of resin and gradually descends after the light source above cures each layer. Bottom up printing, also referred to as inverted SL, lowers the build platform to reach the vat of resin and cure each layer as the platform ascends.
Powder Bed Fusion (PBF)
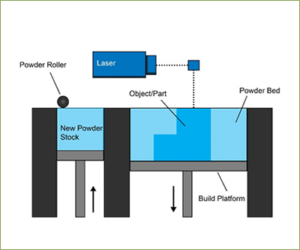
Powder bed fusion (PBF) is a useful method of additive manufacturing that utilizes a powder substrate to create 3D objects. A roller spreads a thin layer of powder across the metal build platform and a laser goes across, selectively fusing the powder to form layers until the model is complete. Selective laser sintering (SLS) typically builds with thermoplastic material and does not require support structures because the parts are supported by the surrounding powder. SLS can create complex geometrical parts, but have a grainy surface and usually require post-processing. Direct metal laser sintering (DMLS) is the same process as SLS, but with metals. Parts start welded to the build plate as the laser sinters the metal powder to the point of fusion. Selective laser melting (SLM) can be used for metals and is a faster process than SLS because it melts an entire layer at once, but it has higher financial and energy costs. SLM is a heat-intensive process, so it requires inert gas to control the melting and support structures to mitigate heat. Metal 3D printing techniques can create objects with high-quality physical properties and adequate surface finish. PBF is a useful method for metal parts, however, it is a cost-intensive and high volume system.
Binder Jetting
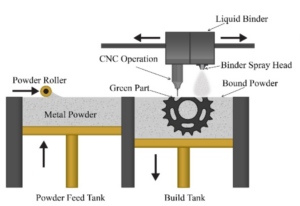
Binder jetting utilizes powdered ceramic, polymer, or metal and adhesives to create 3D models. A fine layer of powder is deposited on the build platform and a printhead binds the particles. Metal parts must be thermally sintered and ceramic/polymer parts can be saturated in adhesive. Binder jetting generally requires post-processing, but it can create large-scale ceramic molds, full-color prototypes, and three dimensional metal structures.
Sheet Lamination
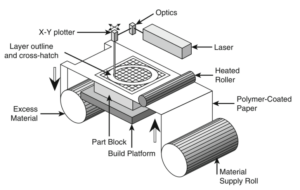
Sheet lamination is an umbrella term for processes that weld or attach pre-cut metal sheets. Ultrasonic additive manufacturing (UAM) can print metal at/near room temperature and uses ultrasonic vibrations to “scrub” thin layers of metal together. The process allows foil to build layer by layer, allowing printers to use different metals on the same part, embed sensors, or create complex internal geometry. Laminated object manufacturing (LOM) alternates layers of material and adhesive to create the final objects.
Direct Energy Deposition (DED)

Direct energy deposition (DED) is a method of additive manufacturing that uses some form of focused thermal energy to fuse powder or wire as it is placed. The material is fed and fused horizontally to create layers, which stack vertically to create the part. DED can use different materials, including ceramics, polymers, and metals. This process is best suited for repairs, rapid prototyping, and functional material structures.
3D printing is an incredibly useful form of additive manufacturing that can utilize a variety of materials and methods to make anything from an early prototype to a finished product. The Makerspace has two FDM printers available for students to use for both school and personal projects.